乳化液是由油、水和乳化剂等成分混合而成的混合物,具有良好的润滑性和冷却性,能够有效提高加工效率。然而,乳化液在使用过程中会受到污染,导致油水分离成为一个重要的技术问题。乳化液油水分离设备的出现,有效地解决了这一问题,帮助企业实现资源的回收利用,降低环境污染。
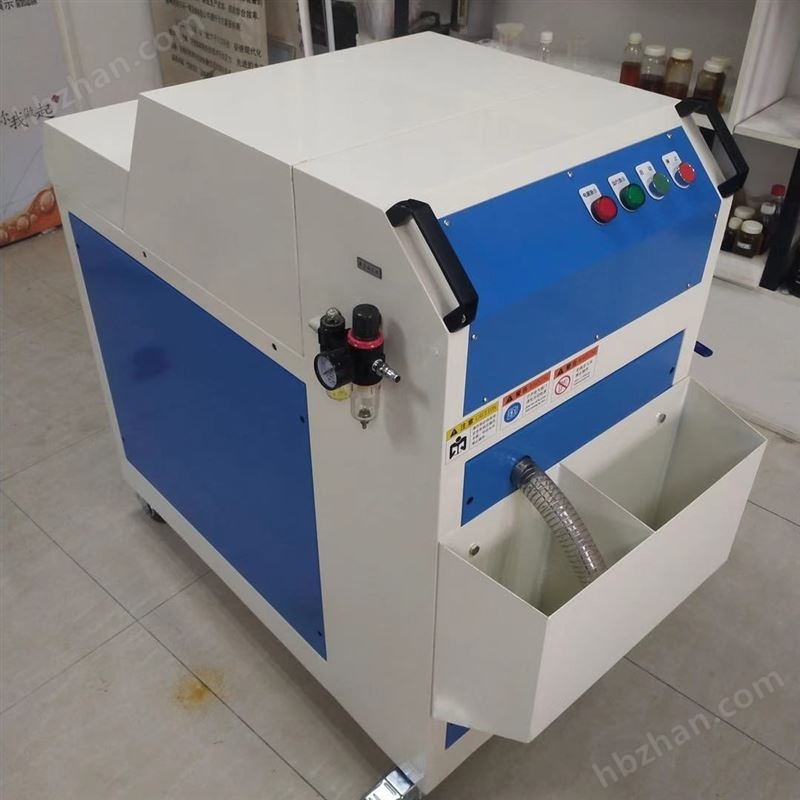
乳化液的分离难度:
1.乳化剂的影响:乳化剂会降低油水界面的表面张力,增加乳化液的稳定性,导致分离困难。
2.微细油滴的存在:乳化液中的油滴直径通常在几微米到几百微米之间,难以通过重力作用自然分离。
3.处理时间要求高:传统的物理分离方法需要较长的时间,无法满足现代工业生产的高效需求。
1.重力分离器:
-原理:利用油和水的密度差异,采用重力作用分离油水。设备通常由进料口、分离室和出料口组成。
-优点:结构简单、操作方便,适合处理大流量的乳化液。
-缺点:分离效果受到油水比例和乳化剂影响,分离效率相对较低。
2.离心分离器:
-原理:通过产生离心力,使油水分离,密度较小的油被排出,而水则从底部排出。
-优点:分离速度快,效率高,能够处理细小油滴。
-缺点:设备能耗相对较高,维护成本较高。
3.膜分离技术:
-原理:利用膜的选择性透过性能,分离油水混合物。常见的膜分离技术有超滤和纳滤。
-优点:分离效率高,能够回收乳化液中的油。
-缺点:膜的污染问题较为严峻,需要定期清洗和更换。
4.加药分离器:
-原理:通过向乳化液中添加化学药剂,改变乳化剂的性质,使油水分离,加药后油水混合物在分离室中重新分层。
-优点:可提高分离效率,适用于处理复杂乳化液。
-缺点:需控制药剂的用量与类型,可能增加处理成本。
为了确保乳化液油水分离设备的优良性能,日常的维护与管理至关重要:
1.定期检查设备:确保设备运行时无异常声响,定期检查分离效果,维护分离效率。
2.定期清洁:特别是膜分离设备和加药设备,需要定期清洗,防止膜污染或药剂结垢。
3.监测处理效果:应对分离后的油水质量进行检测,确保满足排放标准或再利用要求。
4.培训人员:加强操作人员的培训,提高其对设备的操作与维护能力,降低故障发生率。